Implementing Carbon Capture in Industrial Processes: Best Practices
- Hüsnü Tolga Eyyuboğlu
- Jan 20
- 9 min read
Updated: Jan 30
Industries such as cement, steel, chemicals, and power generation are some of the largest emitters of CO2. Unlike other sectors, reducing emissions in these industries is challenging due to process-related emissions that are difficult to eliminate. Carbon capture offers a solution by capturing CO2 at the source and either utilizing it for valuable products or storing it permanently underground.
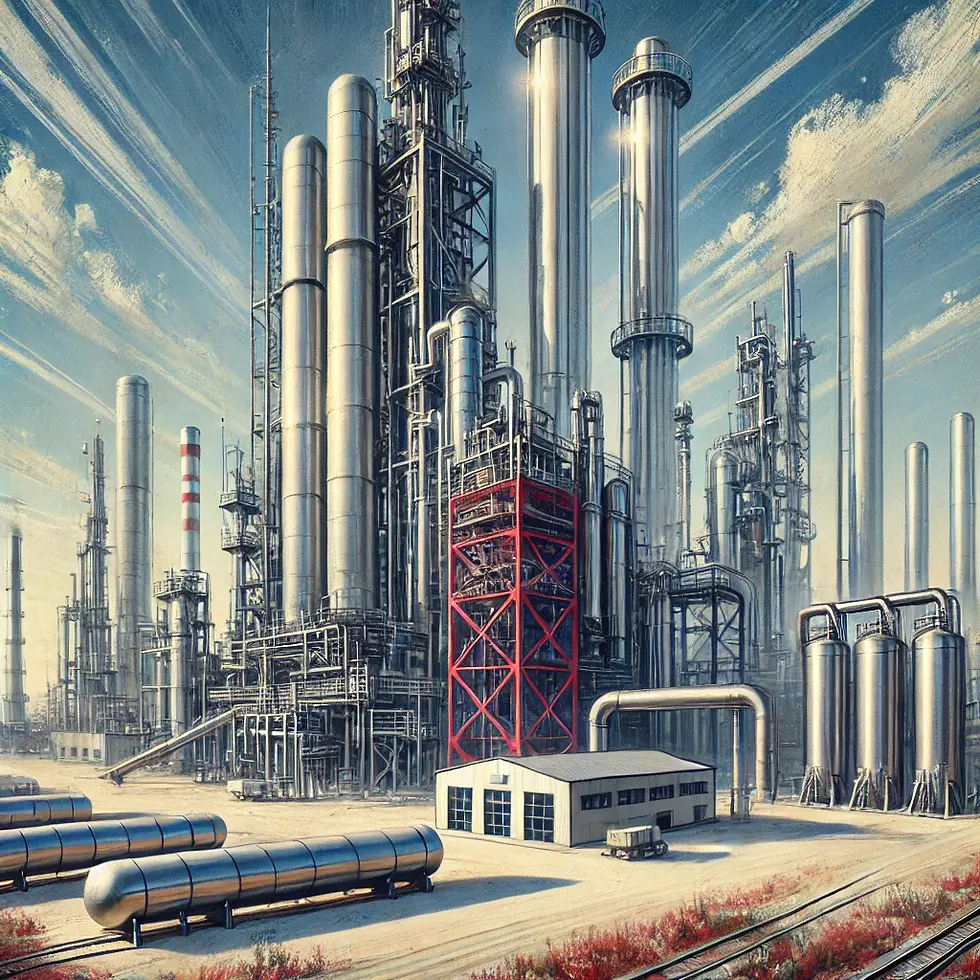
By incorporating carbon capture into industrial operations, businesses can:
Reduce greenhouse gas emissions.
Enhance energy efficiency.
Meet regulatory requirements and achieve sustainability goals.
Create opportunities for CO2 utilization in new markets.
Case Studies of Successful Implementation
1. Petra Nova Project (USA)
The Petra Nova Project conducted extensive feasibility studies before implementation to evaluate technical, economic, and environmental aspects. The emission profile analysis focused on capturing CO2 emissions from the WA Parish coal-fired power plant, identifying an emission volume of 1.4 million tons of CO2 per year. The project chose post-combustion carbon capture technology as it was ideal for retrofitting existing coal-fired power plants, utilizing amine-based solvents to absorb CO2 from flue gas. Economic analysis revealed total project costs of $1 billion, partially funded by the U.S. Department of Energy with a contribution of $190 million. Revenue generated from enhanced oil recovery (EOR) operations helped offset operational costs. Additionally, an environmental impact assessment demonstrated significant CO2 emission reductions and minimal ecological disruption.
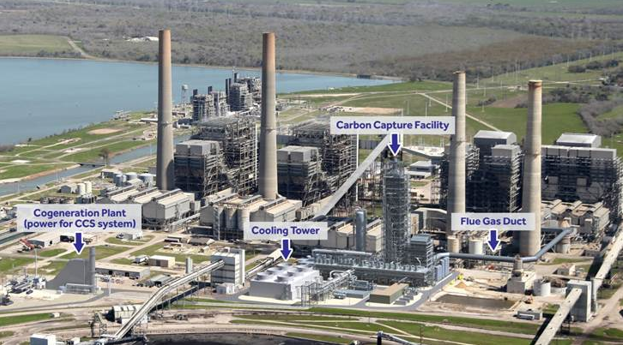
Petra Nova employed post-combustion carbon capture technology, making it compatible with the existing WA Parish plant’s flue gas streams. The project used Mitsubishi Heavy Industries’ KM-CDR Process™ with proprietary solvents to capture CO2 efficiently, achieving a capture efficiency of up to 90%. This technology was selected for its compatibility with retrofitting applications and robustness. Although emerging technologies were not utilized, the project successfully demonstrated scalability and effectiveness.
Integration of the capture system into the existing plant operations was achieved with minimal disruptions. Heat recovery was facilitated through a dedicated natural gas-fired boiler that generated steam for the amine regeneration process, reducing the energy demands on the primary plant. Process adjustments ensured optimal CO2 concentration for capture, and the overall energy penalty was minimized by using dedicated energy sources to meet the system's demands.
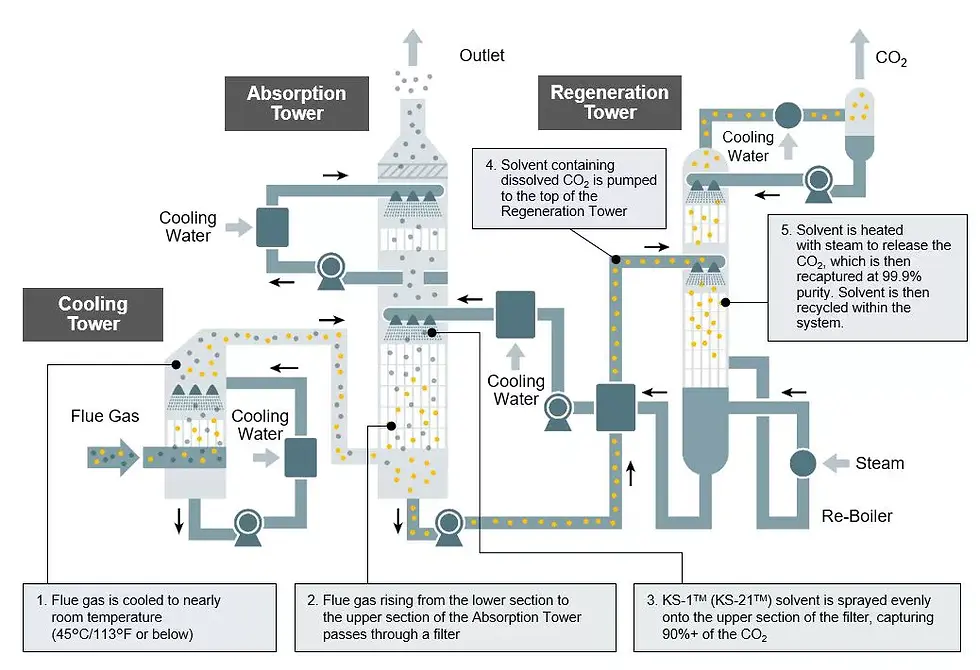
The project included robust infrastructure for CO2 transport and utilization. A 12-mile pipeline was constructed to transport captured CO2 to the West Ranch oil field, where it was used for EOR to increase oil production. While geological storage was not a primary focus, the project’s utilization pathway showcased the economic viability of CO2 use in industrial applications.
The project’s success relied heavily on collaboration among multiple stakeholders. Compliance with U.S. regulatory frameworks and securing necessary permits were prioritized. Community outreach efforts educated local populations about the benefits of CO2 capture and utilization, garnering public support. Industry partnerships with NRG Energy, JX Nippon Oil & Gas Exploration, and the U.S. Department of Energy provided shared funding and technical expertise.
Financing was secured through a combination of public-private partnerships and government incentives. The project received $190 million in funding from the U.S. Department of Energy’s Clean Coal Power Initiative. Cost-sharing between NRG Energy and JX Nippon ensured financial feasibility, and while the primary revenue stream came from EOR operations, the project underscored the potential for carbon credit trading in future initiatives.
Petra Nova established a comprehensive monitoring, reporting, and verification (MRV) framework to ensure transparency and accountability. CO2 capture rates and injection volumes were continuously tracked, and performance metrics were regularly reported to stakeholders and regulatory agencies. Third-party audits validated the reported data, ensuring compliance with environmental and operational standards.
In conclusion, the Petra Nova Project exemplified adherence to best practices for carbon capture implementation. Its use of post-combustion technology, effective process integration, robust infrastructure, stakeholder collaboration, and transparent MRV processes demonstrated the feasibility of large-scale carbon capture. However, the project’s reliance on enhanced oil recovery and challenges with high operational costs highlight the need for further advancements in cost efficiency and scalability for broader application.
2. Norcem Cement Plant (Norway)
The Norcem Cement Plant in Norway has been a pioneering facility in the implementation of carbon capture technologies within the cement industry. A comprehensive feasibility study was conducted to assess the technical, economic, and environmental aspects of the project. This included an emission profile analysis that focused on the substantial CO2 emissions inherent to cement production processes, particularly from the calcination of limestone and combustion of fuels. The feasibility study also explored various carbon capture technologies, ultimately selecting amine-based post-combustion capture due to its suitability for retrofitting onto existing cement plants. Economic analysis evaluated both capital expenditure and operational costs, as well as potential revenue from CO2 utilization, while an environmental impact assessment highlighted significant reductions in greenhouse gas emissions without major disruptions to the surrounding ecosystem.
The Norcem Cement Plant's carbon capture system is designed to capture up to 400,000 tonnes of CO2 annually, making it one of the most advanced initiatives in the cement industry.
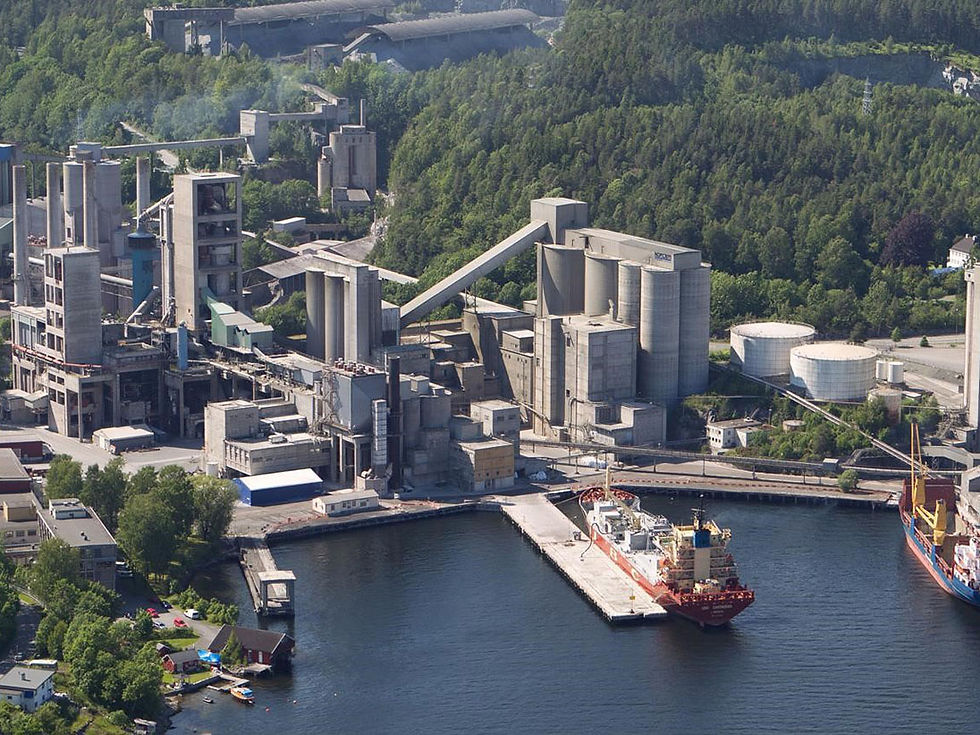
The choice of technology was critical for the project’s success. Post-combustion capture was deemed the most appropriate due to its compatibility with the plant’s existing setup and its ability to handle the relatively low CO2 concentrations in the flue gas. The use of amine-based solvents allowed for high capture efficiency and alignment with the plant’s operational demands. While the project explored emerging technologies like solid sorbents and membranes, these were not adopted due to their developmental stages and lack of scalability for the plant’s requirements.
Process integration was carefully optimized to ensure minimal disruption to the plant’s cement production. Heat recovery systems were implemented to utilize waste heat from the cement kilns for solvent regeneration, reducing the energy penalty of the capture process. Adjustments to combustion processes helped enhance CO2 concentrations in the exhaust gases, which improved the capture system’s efficiency. These measures minimized the overall energy demand and operational costs, making the project more economically viable.
Building robust infrastructure for CO2 transport, storage, and utilization was another focus area for Norcem. The captured CO2 is transported via pipelines to secure geological storage sites, primarily in the North Sea’s saline aquifers. These storage facilities have been extensively evaluated for their safety and capacity, ensuring long-term containment of CO2. Additionally, the project explores potential utilization pathways, including the use of CO2 in building materials and other industrial applications, although this remains a secondary focus compared to storage.
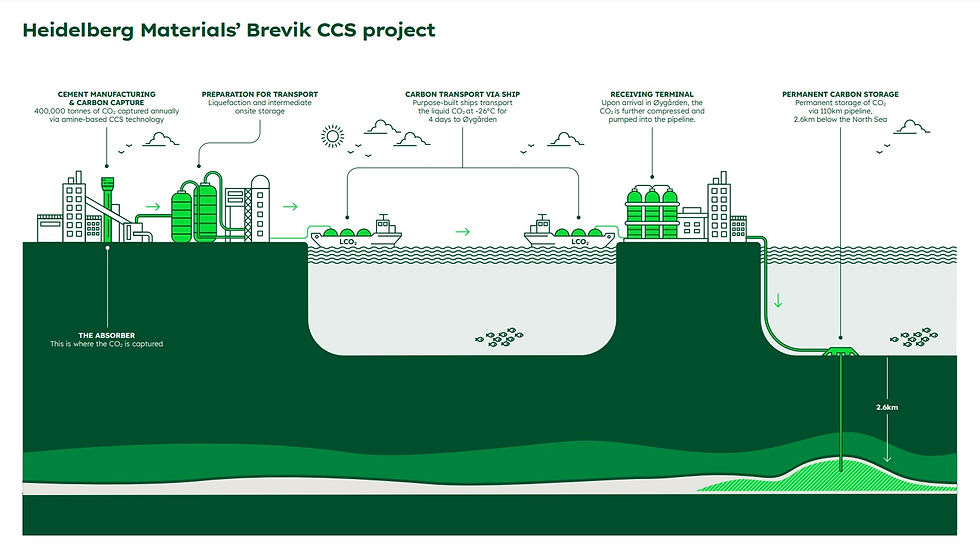
Stakeholder engagement was a cornerstone of Norcem’s approach. The project involved collaboration with government agencies, industry leaders, and local communities. Regulatory compliance was ensured by working closely with Norwegian authorities to secure necessary permits and align with national climate goals. Community outreach programs educated local residents about the project’s benefits and safety, fostering public trust and acceptance. Partnerships with research institutions and other industrial players facilitated knowledge sharing and cost-sharing for CO2 transport and storage infrastructure.
The estimated total cost of implementing the carbon capture system is approximately €400 million.
Securing financing was a significant challenge due to the high capital costs of the project. The plant leveraged government incentives, including grants and subsidies from Norway’s Ministry of Petroleum and Energy, as well as funding from the European Union’s Innovation Fund. Public-private partnerships further supported the project, distributing financial risks among stakeholders. While carbon credits are not yet a major revenue stream for the project, they represent a potential future avenue for additional income.
3. Quest Carbon Capture and Storage Project (Canada)
The Quest Carbon Capture and Storage (CCS) Project in Canada represents a benchmark in the deployment of large-scale CCS technologies. Quest identified post-combustion capture as the most suitable technology due to its compatibility with the facility’s flue gas streams. The economic analysis revealed that the project’s initial capital cost of CAD 1.35 billion would be supported by substantial government funding, while an environmental impact assessment underscored the project’s potential to capture and store over one million tonnes of CO2 annually, significantly reducing emissions.

Quest’s selection of post-combustion capture technology was driven by its ability to efficiently process CO2 at high concentrations. This choice was further supported by the use of Shell’s CANSOLV™ CO2 capture system, which employs amine-based solvents to achieve high capture efficiencies. While alternative technologies such as oxy-fuel combustion and pre-combustion capture were considered, these were deemed less viable due to higher integration complexities and incompatibilities with existing operations. Emerging technologies were not adopted but remain a focus for potential future optimization.
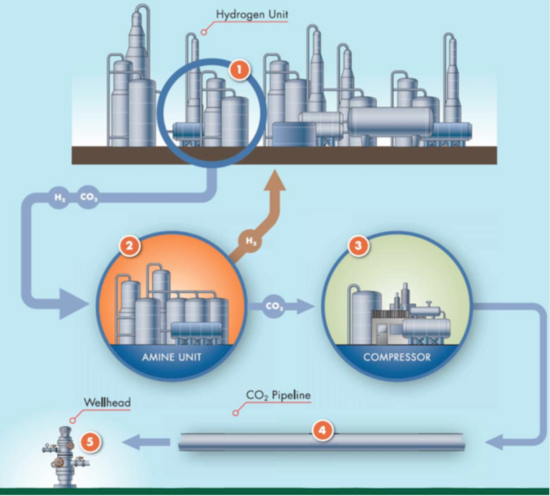
The integration of Quest’s CCS system with the Scotford Upgrader was designed to ensure operational efficiency and minimal disruption. Waste heat from the facility’s operations was effectively utilized for solvent regeneration, significantly reducing the energy penalty associated with the capture process. Modifications to process parameters also increased the CO2 concentration in flue gases, optimizing the capture efficiency. These measures minimized operational costs and ensured seamless integration with existing infrastructure.
A robust infrastructure was developed to support CO2 transport and storage. Captured CO2 is transported through a 65-kilometer pipeline to secure geological storage sites in the Alberta Basin. These storage facilities, consisting of deep saline aquifers, have been rigorously assessed for long-term containment and safety. While the primary focus of Quest is on storage, the project also considers future opportunities for CO2 utilization in industrial applications, such as enhanced oil recovery or the production of carbon-based materials.
Partnerships with industry leaders, such as Shell and the Alberta government, were instrumental in sharing costs and advancing technological development.
Quest benefited from substantial public funding, with CAD 865 million provided by the governments of Canada and Alberta. These contributions significantly reduced financial risks for the project’s stakeholders. Moreover, the project highlights the potential for generating additional revenue through carbon credits, though this has not been fully realized at its current stage.
Common Challenges and Solutions
Challenges:
High upfront capital costs.
Energy intensity of capture processes.
Public perception and acceptance.
Regulatory hurdles and uncertainty.
Solutions:
Invest in research and development to lower costs and improve efficiency.
Utilize renewable energy to power carbon capture systems.
Conduct transparent public outreach to build trust and awareness.
Advocate for clear and consistent regulatory frameworks.
As we look to the future, critical questions arise: Are we truly prepared to scale carbon capture to the levels needed to combat climate change effectively? How can we make these technologies more affordable and accessible to smaller industries? What role will emerging innovations, like direct air capture and advanced materials, play in shaping the next decade of industrial decarbonization?
Furthermore, how will evolving policies and global collaborations influence the pace of adoption? Will carbon capture become an essential part of every industrial process, or will alternative solutions take center stage?
The answers to these questions lie in our collective ability to push boundaries, challenge the status quo, and embrace both innovation and collaboration. As stakeholders in this journey, are we ready to take the bold steps necessary to make carbon capture an everyday reality?
Implementing carbon capture isn’t just about compliance; it’s about securing a sustainable future for businesses and the planet. The success stories of projects like Petra Nova, Norcem, and Quest prove that carbon capture is a viable solution when approached strategically. Investing in the right technologies, fostering stakeholder collaboration, and staying informed on policy changes are critical steps toward success.
As industries take bold steps towards decarbonization, those that act now will lead the way in shaping a low-carbon future. Let’s embrace the challenge, innovate continuously, and turn sustainability goals into reality—because the future of our planet depends on it.
댓글